王世超
(厦门洛矶山石油集团有限公司)
摘 要:介绍了冶金企业连铸及轧钢设备在高温及有水存在的环境下的几种润滑脂的应用现状,并对使用当中的问题及发展方向进行了探讨。
主题词:冶金;连铸;轧钢;润滑脂;进展
1 前言
在发达国家,冶金产业一直是润滑脂用量Z大的产业,在我国也不例外。同时,由于冶金企业生产流程较长,设备也较为繁杂,再加上其特殊的工况条件(高温、多水、多尘、重载),使得其对润滑脂的要求相当严苛。关于冶金行业用脂的特征及现状,笔者曾经在有关文章中作过介绍
[1,2],在此不详赘述。以下,仅就冶金行业用润滑脂近几年的发展状况及趋势做一探讨。
2 高温润滑脂
近年来,随着国外先进设备的大量引进,对润滑脂的要求日渐严格。在高温润滑部位,原用的通用锂基润滑脂和极压锂基润滑脂已基本被耐温性能更好的复合铝、复合锂以及聚脲脂所取代。就以上三种脂的综合性能来讲,无疑是以聚脲脂Z为优良,但因其都具有本身所独有的优劣点,以后在冶金企业的高温设备润滑方面必将共存一个很长的时期。
2.1烧结机专用脂
国内冶金企业中,历来在烧结机上沿用合成复合铝基润滑脂。但合成复合铝基脂在应用中存在致命缺陷,一是由于本身的硬化造成各种性能(主要是润滑性)的大幅度下降;二是由于泵送性差而使各润滑点不能得到充分、合理的润滑。为此,自90年代初起各企业开始尝试使用天然复合铝基脂。由于该脂具有良好的低温泵送性、润滑性及抗水性,加之本身无硬化,因此在应用中取得了较为满意的结果。在此基础上,本公司开发出了价格低廉,且综合性能比复合铝基脂更为优越的聚脲型烧结机专用脂,该脂在抗磨损性、密封性等各方面均有了更大提高,经在承钢、宣钢等单位应用证明,该脂能更为有效地延长滑道与轴承的使用寿命,降低烧结机的有害漏风率和综合能耗指标,取得了相当满意的应用效果。表1所列出的即是聚脲型烧结机脂的技术条件。
表1 烧结机专用聚脲脂质量指标
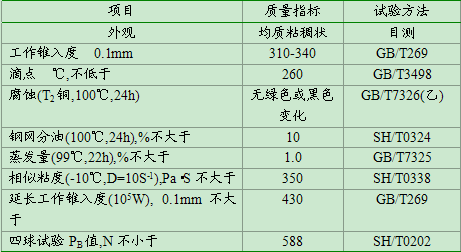
2.2连铸机用润滑脂
在连铸设备中,采用脂润滑的有钢包回转台、结晶器、引锭杆、二冷区夹辊及侧导辊、拉矫机、传送辊道及切割机等部位,这些部位共使用内径为50-150mm的自动调心滚动轴承300-400个,轴承受表面温度高达800℃以上的铸坯的辐射热及传导热,每小时几百乃至上千立方米的冷却水以及大量氧化鳞皮及尘埃侵入的影响,润滑条件非常恶劣。同时,导辊部位由于钢的自重及矫直过程还需承受相当的负荷。
近年来,连铸设备用脂已基本完成了由极压锂基脂、通用锂基脂向复合皂基脂的转化过程。也正如笔者以前所论述的
[1]那样,较高档次的复合铝基脂和聚脲脂、复合磺酸钙基脂等也已获得了广泛应用。与日、美、德等发达国家相比,我们在连铸设备用脂的差距已在明显缩小。但同时也应指出,复合铝基脂的高温碳化和聚脲脂的硬化问题必须引起注意。另外,目前国内各润滑脂生产企业所生产的聚脲脂、磺酸钙基脂在品种、工艺上各不相同,产品的质量档次也有明显差异,其在应用效果上的差别也就显而易见了。
2.3关于聚脲基润滑脂
聚脲是指含有脲官能团(—HNCONH—)的一类化合物的总称,凡以此类化合物稠化基础油而制得的润滑脂均可称为聚脲脂。一般来讲,聚脲应以异氰酸酯和胺类反应制得,其中,单异氰酸酯和单胺作用生成单脲,二异氰酸酯和单胺或单异氰酸酯和二胺反应生成二脲,二异氰酸酯和二胺单胺共同反应生成四脲......。异氰酸酯的结构式为R—NCO,而胺类的结构式为R'—NH
2,两式中的R、R'所代表的烃基可分别为脂肪烃、脂环烃或芳香烃。因此,生产聚脲脂的原料本身可说是千差万别,不一而足。其所生产的聚脲脂的品质差异也就可想而知了。
目前,国内生产聚脲脂所采用的异氰酸酯大体上是TDI(甲苯二异氰酸酯)或MDI(二苯甲烷-4,4-二异氰酸酯),然后用不同的胺类与之反应制做二脲脂或四脲脂。由于所采用的胺类各不相同,所得到的聚脲脂产品性能也相差较大。其中,用脂肪族胺所得到的脂稠化能力较好,而芳香族胺所得到的脂抗剪切能力更强一些
[3]。应该说,无论是二脲脂还是四脲脂,只要配方和生产工艺合理,均有可能获得性能优良的润滑脂。在70年代,曾有四聚脲Z有前途一说,但因工艺条件难于控制,目前在国内外的发展及应用上四脲脂均远不如二脲脂,这一点在目前的国内产品性能对照及应用状况上也都得到了证明。表2所列出的是本公司生产的二脲型连铸机脂的技术要求。
表2 二脲型连铸机脂质量指标
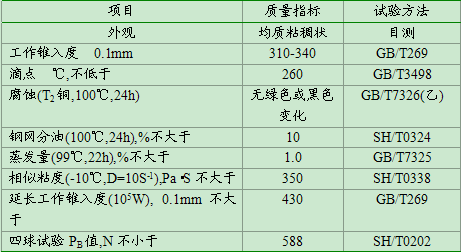
另外需要说明的是,适宜的工艺条件对聚脲脂的结构形成也起着关键作用。因为聚脲本身具有典型的旋光异构现象,只有通过合理调整工艺路线,使得聚脲真正形成“对称式”的稳定结构,进而形成致密、微细的巢状骨架状态
[3],才能保证其各种性能,尤其是剪切安定性及抗水性。如何根据不同配方确定合理的生产工艺将是各聚脲脂生产厂家所应努力探讨的课题。
2.4关于磺酸钙基润滑脂
毫无疑问,磺酸钙基脂具有着出色的性能,但到目前为止,这种性能的表现也只限于国外进口产品。也就是说,国内的产品并不是很过关!
早在十几甚至二十年前,笔者在天津津脂研究所任职时就曾对磺酸复合钙基脂有过涉猎,但可惜的是,直到目前国内对磺酸钙基脂的生产也并未找到Z好的办法。国内大多数是采用购买高碱性磺酸钙作为稠化剂的方法,不同碱值、甚至不同工艺下的磺酸钙作出的润滑脂都有着很大的差异。更何况,一般国外磺酸钙基脂的生产工艺与普通润滑脂有着根本不同,所以到现在生产不出高质量产品也就不足为奇了。
2.5炉前辊道轴承用润滑脂
除去良好的高温性及密封性外,炉前辊道轴承用脂所需要的Z为重要的特性应是其抵抗冲击负荷的能力。这一点上,一般通用脂类是达不到的,建议在该部位采用极压复合锂、极压复合铝或聚脲脂,必要时还需加入固体抗磨剂如MoS
2粉等。
3 抗水性润滑脂
无论是在国内外,抗水润滑脂的发展都是与轧钢设备的发展紧密相连的。以下,仅就几种轧钢设备常用润滑脂的问题点及解决方向做一探讨。
3.1复合锂基润滑脂
目前国内用做轧辊脂Z多的是复合锂基润滑脂,但多年的实践证明,复合锂基润滑脂在应用中存在着一定缺陷,主要体现在油品在高速旋转的轧辊轴承中没有足够的附着力,不能抵抗由于轴承的高速旋转而带来的巨大离心力,因而会较轻易的被从轴承中甩出,从而失去润滑效果。某些厂家曾试图用添加增粘剂的方法予以改进,但因润滑脂内部各组分的性能、密度等均有很大差异,加之添加剂之间缺乏应有的配伍性,在大离心力的作用下内部结构离析,造成上述问题仍不能解决。为此,本公司通过优化产品配方,选择适宜的基础油和添加剂制成了目前的复合锂型和聚脲型轧辊轴承脂,取得了一定的应用效果。表3所列出的是聚脲型轧辊轴承脂的技术要求。
表3 聚脲型轧辊轴承脂质量指标

另外,复合锂基脂的机械安定性及抗水性较差,而硫铅型极压添加剂的添加就更加重了这一现象。为此,本公司通过优化配方,选用优质进口添加剂研制出了机械安定性及抗水性极强的极压复合锂基脂,其结果示于表4。
表4 耐水性极压复合锂试验结果
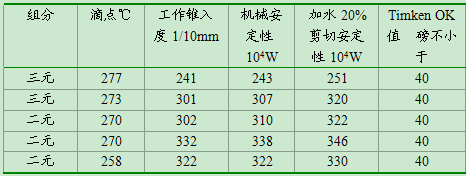
3.2极压锂基润滑脂
轧钢系统相当一部分润滑部位都在沿用极压锂基润滑脂,并且,由于该脂具有良好的极压性和泵送性,一直在冶金设备用脂中处于不可动摇的地位。但随着生产连续化要求的增加和负荷的增强,某些润滑部位已开始感受到了极压锂基脂的不适应。究其原因可能有两点:1)硫铅型极压添加剂使得锂基脂本就不强的抗水性变得更差,在大量冷却水冲刷下润滑脂很难在润滑点停留,因此在润滑部位形成干摩擦,进而烧损轴承。2)35磅的承载能力(Timken OK值)不能达到设备负荷要求,在高极压状态下油膜发生破损,进而烧损轴承。因此,解决极压锂基脂的问题的根本在于同时提高其承载能力及抗水性。为此,本公司研制出了耐水性极压润滑脂,该脂在保持了优良的低温泵送性的同时,极大地提高了抗水性及耐压性,其具体技术要求见表5。
表5 耐水性极压润滑脂的技术要求
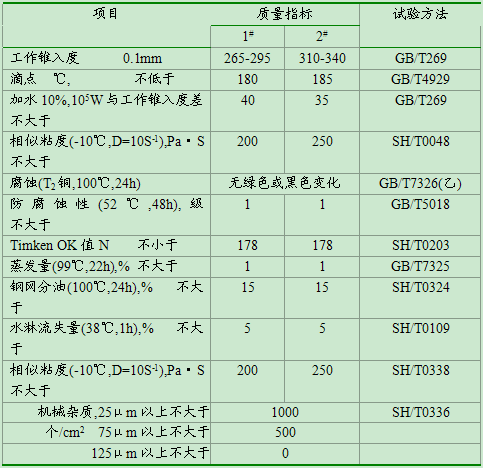
3.3齿形联轴节用润滑脂
在高速轧机上,齿形联轴节(齿接手)的转速可高达几千转乃至上万转,因而会产生相当大的离心力;加之齿接手是依轴心偏移使齿的接触状态发生变化,从而使齿面与齿顶间发生滑动,因此润滑条件是相当严格的4。与轧辊轴承脂相类似,齿接手脂所要求的Z重要的特点就是其抵抗巨大离心力的能力,同时还需要有极强的极压抗磨性及抗水性。
本公司研制齿接手专用脂的出发点是:选择适宜的基础油、稠化剂和添加剂,使其各组分之间保持良好的亲和力,同时采用进口添加剂赋予其优良的粘附性与极压抗磨性。目前所试制的样品已进入评定阶段,相信在齿接手上取代进口脂的日子已为期不远了。
4 结束语
限于篇幅,笔者仅就几种冶金设备常用润滑脂的现状,应用中存在的问题以及发展方向做了简略论述,希望能对冶金设备的润滑事业有所助益,如此笔者将不胜欣慰。
参考文献:
[1]陆志中、王世超等金属学会年会论文集,1994.12 上海
[2]王世超、刘清华等五届连铸学术会议论文选,1995 杭州
[3]王世超、郭宝茹摩擦学年会论文选,1994.10 武汉 P67-70
[4]欧风合理润滑技术手册,1993.5 P452
来源:《润滑油》2001年第6期