颜振现 张玉荣 张鹏飞
(邯郸钢铁公司线棒材厂,河北邯郸 056015)
摘 要:针对高速线材生产中,精轧机辊轴及隔套锁紧螺母存在的问题进行分析,提出了改进措施,取得了较好效果。
关键词:线材;精轧机;辊轴;隔套;锁紧螺母;改进
1 前言
邯钢高速线材生产线是中国较早的一条高速线材生产线,1986年开始建设,1987年投入生产,由英国阿西洛公司的引进。该生产线的精轧机采用英国阿希洛10架,45°无扭顶交精轧机。在轧机辊轴端安装辊环来实现轧制,Z大轧制速度75m/s。
2 精轧机存在的问题及原因分析
2.1 辊轴锥度根部断裂
图1为改进前辊轴R8圆弧根部时常出现断裂现象,尤其是进入精轧机架轧机,发生断裂现象较多,一年约有10次。分析其原因是辊轴锥度根部R8圆弧曲率半径较小,应力较集中,另外,架轧机距前面预精轧机距离较远,冲击力大,负荷也较大,发生辊轴锥度根部断裂现象也较多。
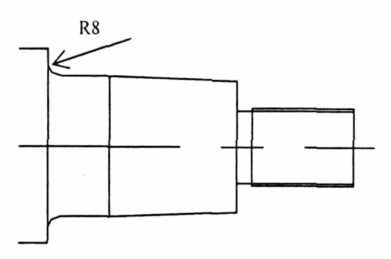
图1 改进前的辊轴锥度根部
2.2 辊轴螺纹根部扭断
图2为改进前退刀槽采用直角形式,因此处应力集中较大,再加上锁紧螺母有预紧力,而且在轧机高速旋转中,在转动惯量作用下,锁紧螺母越来越紧,导致辊轴螺纹根部扭断。

图2 改进前的辊轴螺纹根部
2.3 辊轴上轴承隔套崩裂
图3为改进前轴承隔套R9圆弧在与辊轴R8圆弧的配合中,由圆弧面接触,再加上轴承隔套的轴向力较大,轴承隔套在圆弧处所受外撑力非常大,经常导致轴承隔套在圆弧处崩裂现象。
3 改进措施
针对精轧机出现的问题,经过分析、研究,对其实施了如下改进。
3.1 辊轴锥度根部
辊轴锥度根部R8圆弧改为R15圆弧,图4为改进后把R15圆弧改为与根部端面相交形式。由于圆弧曲率半径加大,根部直径加粗,抗剪强度增强,应力集中相对减少,从而提高了根部强度。
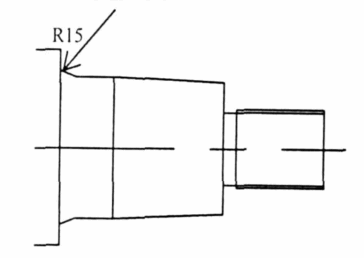
图4 改进后的辊轴锥度根部
3.2 辊轴螺纹根部
辊轴螺纹根部退刀槽由直角形式改为圆弧形式,图5为改进后相对减少应力集中,提高了根部强度,减少螺纹根部承受力矩,减少辊轴螺纹根部扭断现象。
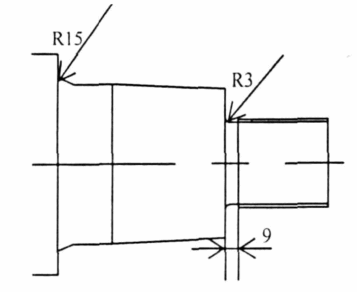
图5 改进后的辊轴螺纹根部
3.3 轴承隔套
轴承隔套改R9圆弧为斜度,图6为改进后原来在圆弧面接触改为锥面,大大减少了轴承隔套在圆弧处所受向外撑力,提高了轴承隔套使用寿命。

图6 改进后的轴承隔套
3.4 锁紧螺母
将锁紧螺母去掉一些多余量,改进前后的比较见图7,重量由615kg改为512kg,大大减少了转动惯量,同时缩短了锁紧螺母伸入锥套长度,避免了因锥套、辊轴及辊座磨损导致锁紧螺母压不紧锥套使辊环耍圈现象。
图7 锁紧螺母
4 效果
经过改进已运行一年多,效果非常好,辊轴锥度根部断裂现象大大减少,由原先的一年10次左右减为1~2次,年可节省辊轴备件费用5万元;而辊轴螺纹根部扭断未在发生,节省费用118万元;轴承隔套消耗年减少约100件,节约费用114万元;并可减少停机时间20多小时,年经济效益达10万元以上。
来源:《河北冶金》总第165期 2008年第3期