刘登发 伍水生
(长丰汽车衡阳风顺车桥有限公司,421001)
摘 要:介绍了轻型越野汽车主减速器的结构特点;讨论了主减速器轴承预紧度及装配调整技巧;针对主减速器齿轮的损坏形式,对该类车型主减速器的故障进行分析。
主题词:主减速器;调整技巧;故障分析
一、轻型越野汽车主减速器轴承预紧度的装配调整技巧
实践说明,轻型越野汽车主减速器齿轮(减速用的螺旋锥齿轮)的使用寿命及运转性能,除与其本身的设计、制造有直接关系外,还受到其支承刚度及装配调整的影响。因此,科学合理地装配调整对减速器的使用寿命和整车的性能起着至关重要的作用。
1、轴承预紧的必要性
轻型越野汽车主减速器的构造如图1所示。
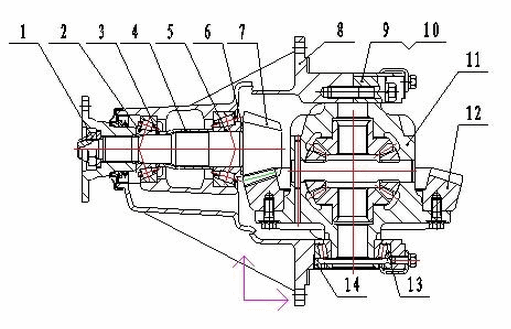
图1
1.主动齿轮螺母;2.主齿前轴承;3.前轴承调整垫片;4.弹性隔套;5.主齿后轴承;6.后轴承调整垫片;7.主动齿轮;8.主减速器壳;9.差速器左轴承;10.左轴承调整螺母;11.差速器总成;12.被动齿轮;13差速器右轴承;14.右轴承调整螺母
理论研究和长期的汽车使用经验已证明,主减速器螺旋锥齿轮副的安装,必须保证其有足够的支承刚性,它是该齿轮副能否平稳啮合,并具有高的使用寿命的重要因素之一。在选择齿轮的支承形式时,必须考虑支承刚性的要求。在实践中,对支承齿轮轴的轴承采取预紧措施,也可以增强支承刚性;同时,轴承预紧还可以消除装配的原始间隙,减缓磨合期甚至正常使用初期的轴承间隙的出现及增大。
图1中的2、5号零件是一对支承着锥齿轮的圆锥滚柱轴承。如通过扭紧锥齿轮轴左端的调整螺母1,给轴承副以预紧力,那么在轴承圆锥滚柱及其内、外圈工作表面之间将产生接触压力。轴承副的作用等价于图2b所示的一对刚度很大的弹簧,因此,接触表面产生弹性变形不可避免。下面分析一下施加预紧力前后,这对轴承对支承刚性的影响。为了研究方便,将其用图2a所示的模型代替。
在图2a中,一根销轴滑套在一固定不动的圆盘的孔内,在其两侧各装有一尺寸和刚性都相同的弹簧。弹簧的一端顶靠在固定不动的圆盘上,另一端则顶靠在可以相对销轴轴向移动的档片上。另外,设两弹簧的自由长度均为110mm,其刚性如图3中的直线1所示。
如果不给上述模型提供预紧力,那么当销轴的一端作用有一轴向力时,此力将通过轴上该端的销钉推动挡片,产生轴向位移。这种位移从一开始就压缩该侧的弹簧,并使另一侧的弹簧完全处于自由状态而不起作用,整个系统的刚性与一个弹簧的刚性完全一致,即按图3中的直线1变化。
如果给系统以预紧力,使两个弹簧分别预先压缩10mm,如图2b所示。然后再在销轴的一端施加轴向力,则在此力的作用下,受轴向力作用其一端的弹簧将在原已预紧的基础上继续被压缩,而不受轴向力作用的另一弹簧,则在原来预紧的基础上逐渐地被松弛,这种情形将一直持续到右侧弹簧恢复到其自由长度为止。而在整个过程中,系统特性将沿着图3中直线2规律变化。也就是说,在图2a给定的预紧条件下,若作用在销轴一端的轴向力为980N,则销轴处于平衡状态时,仅相应右移5mm;若作用力增大到1960N,销轴平衡时相应右移10mm,如所施加的轴向力继续增大,那么,系统的刚性将沿图3中与直线相连的虚线变化。
对系统采取预紧措施后,轴承的轴向支承刚性将会增大。由于轴承的刚性是非线性的,圆锥滚柱轴承的轴向变形与轴向载荷的0.75次方正比(见图4中曲线2),所以系统的刚性增加要比模型更为显著。在一定的范围内,预紧措施还能消除在轴向力上由于一个轴承的弹性变形而产生的轴向间隙,这是因为中间的弹性隔套4及另一端轴承的弹性恢复量会补偿可能出现的间隙。另外,在使用过程中,由于轴承中各零件的磨损,也会出现轴向间隙,但预紧后弹性隔套及轴承的弹性恢复过程将在一定程度上对此加以弥补。
2、轴承预紧度的调整
在轻型越野汽车主减速器的装配过程中,共有两处轴承的装配预紧度需检查、调整。
首先,要检查、调整主动螺旋锥齿轮轴7前后轴承的预紧度。
一般来说,轴承的预紧度用旋转齿轮所需的力矩来检查。检查前,轴承应润滑,且轴承内圈应当正、反两个方向相对于外圈各旋转不少于5圈,以便于其中的各圆锥滚柱处于内、外圈滚道中的正确位置。同时,也有利于确保重复性检测数据的真实性和可靠性。
按规定,以190~250N•M的力矩拧紧主动螺旋锥齿轮凸缘上的螺母,使弹簧秤的拉力方向垂直于凸缘时的弹簧秤拉力值。将此拉力值乘以凸缘螺栓孔至花键孔中心的距离后,即可得知用于转到主动螺旋锥齿轮所需力矩值,即表征该项轴承预紧度的具体数值(未装主动齿轮油封状态下该力矩较为合适经验值为1.10~2.3N•m)。
如果检查结果不符合上述经验值,则应调整主动螺旋锥齿轮轮轴7的轴承预紧度。由图1可知,在按规定拧紧主动螺旋锥齿轮凸缘螺母后,安装在减速器壳8中的轴承座中的两圆锥滚柱轴承外圈分别被轴承座中加工出的凸起限定了位置,而影响装配紧度的是两轴承内圈之间的距离,此距离大小由靠近凸缘一侧的圆锥滚柱轴承内圈与主动螺旋锥齿轮轴7凸肩端面之间前轴承调整垫片3的厚度和弹性隔套4的长度共同决定。减少该组垫片的厚度或弹性隔套的长度、拧紧凸缘螺母后,两轴承内圈之间的距离缩短,轴承预紧度增加;反之,两轴承内圈之间的距离加大,轴承预紧度较小。
其次,要检查、调整主、从动螺旋锥齿轮轴承预紧度。
由图1可见,该处的两圆锥滚子轴承安装就位后,其外圈分别紧靠轴7两侧加工出的定位凸肩端面上,轴承预紧度的大小,取决于两轴承外圈的轴向距离,亦即取决于主减速器壳8两侧调整螺母10和14之间内端面之间的距离。拧紧两轴承盖调整螺母10和14时,两轴承外圈之间相互靠近,预紧度增大;反之,两轴承外圈相互远离,轴承预紧度减小。
在某些修理场合,检查此项轴承预紧度时,可采用以下经验方法,即固定主动齿轮轴不动然后用双手上、下握住从动螺旋齿轮轮盘两侧,沿其轴径向用力晃动齿轮,如此时手感无轴向间隙感时,且该齿轮能够灵活转动,则认为轴承预紧度合适。
若限于具体条件,无法实施上述测量,也可按下述方法调整:从差速器轴承没有轴向间隙时起,将左侧调整螺母向内拧紧一个环外端止动凹槽的位置,而另一侧的调整螺母向外相应旋出一个凹槽位置即可。
轴承的正确预紧会带来很多好处,但预紧度不宜过紧。否则,会使之减速器传动效率变低,并加速轴承磨损和其他损伤。在使用中,在汽车行驶一段时间后,停车检查主减速器壳体外部的温升情况,如果装配轴承处的壳体外表面过热,那么该处轴承预紧度过大,需要及时加以调整。
二、主减速器螺旋锥齿轮齿面接触区的装配调整
轻型越野汽车主减速器螺旋锥齿轮齿面接触区和齿侧间隙的调整,应在圆锥滚柱轴承预紧正确调整之后进行。
轻型越野汽车主减速器,设计时已在齿轮支承的结构上保证了主、从动螺旋锥齿轮能够进行各自轴向位置的调整,而正确的齿面接触区和齿面侧间隙的获得,正是依赖上述齿轮轴向位置的调整而实现的。
在图1中,若增加主动螺旋锥齿轮7前后轴承垫片3与6的厚度,则主动螺旋锥齿轮沿其轴7的方向远离从动螺旋锥齿轮12;反之,则两者相互靠近。另外,差速器轴承预紧度的调整先将主被动齿轮的间隙调整为零,然后按前述要求将两侧差速器轴承调整螺母预紧至一定程度(手感测量或测量主动齿轮凸缘孔处的扭矩),手感法的测量方法如上所述,若用扭矩法测量(扭矩经验值在3.0~4.3N•m)的改进矩调整也后,再调整主、被动齿轮的间隙,该间隙值一般控制在0.18-0.23mm之间,但在调整中应确保左右两侧螺母旋进和旋出的圈数相等。否则,将破坏已调整好的轴承预紧度。
若检查发现从动螺旋锥齿轮在主动螺旋锥齿轮沿汽车前进或倒车方向旋转时,其轮齿凸面(前进方向)和凹面(倒车方向)的齿面接触区均位于轮齿大端,则首先应将左轴承调整螺母10向外放出半圈,然后,再将右轴承调整螺母向内旋入半圈这样,就可在按规定扭矩拧紧左、右轴承盖螺母后,一方面维持了预紧度,一方面使从动螺旋锥齿轮向主动螺旋锥齿轮靠近,从而使从动锥齿轮齿面接触区向齿小端移动,趋于正确位置。若由于移动从动螺旋锥齿轮导致齿轮间的间隙变小,则可通过从动齿轮的轴向位置以满足齿侧间隙0.18~0.25mm的装配要求。
在目前生产条件下,螺旋锥齿轮一般是经过配对研磨与检验的,即在机加工完成后配对进行齿面研磨,并在滚动检验机上检验成对齿轮的齿面接触区及噪音、从动螺旋锥齿轮转动一周时的齿侧间隙变动量及齿侧间隙的极限值。因此,在减速器装配或修理过程中,不允许将主、从动螺旋锥齿轮副中某一件单独更换,也不允将原配对关系打乱。
三、减速器常见故障分析
轻型越野汽车的主减速器在工作中,要承受很大的变动载荷。经长期使用后,主减速器的齿轮、轴承等零部件将产生不同程度的损坏,主减速器壳也可能产生变形,影响各相关零部件的正确位置关系。这些都将使总成工作状况恶化,以致出现不正常的响声、发热、传动效率下降等故障,甚至不得不停驶修理。
1、螺旋锥齿轮与斜齿圆柱齿轮的损坏
在正常情况下,该主减速器螺旋锥齿轮副的使用寿命可达4×10
5km以上,齿轮的损坏形式主要是疲劳破坏。其中,尤以主动斜齿圆柱齿轮的表面疲劳剥落为甚,而弯曲疲劳断裂次之,其他不正常的轮齿磨损也较为常见。
齿面的疲劳点蚀及剥落,是渗碳齿轮的主要破坏形式。据统计,正常情况下,大约有70%的主减速器齿轮都是因此而报废的。由于轮齿在工作承受很大的表面接触应力,因此常在节圆附近形成极小的齿面裂纹,并进而发展成浅凹坑或麻坑,即点蚀。一般这种损坏率先发生在几个齿上,随着齿轮的继续工作,逐渐增大,甚至使齿面成块剥落,产生噪音。较大的动载荷,Z终导致轮齿迅速损坏或折断。在汽车日常使用中,如果长期超载,或由于维修调整不当造成或齿面接触区位置严重不当,都将使局部齿面接触压力大幅度提高,促使齿面点蚀和剥落现象。
轮齿断裂主要是由疲劳和过载引起。装配过程中齿侧间隙调整不当、安装刚度不足(即轴承预紧度不足)、安装位置不对等原因,使齿面接触区位置偏向一端,造成应力集中,常使轮齿沿斜向产生局部齿端面过载断裂。
主减速器齿轮的不正常磨损,主要是零部件运转传动中产生的剥落颗粒,装配、修理过程中带入的外部杂质、未清除干净的型砂、氧化皮以润滑油中混入的磨料颗粒等引起的磨损。由此可见,主减速器生产及修理装配时,重视产品清洁度的控制,使用正确牌号的润滑油,以及在走合期和正常使用期内按规定的里程进行维修保养,清洗更换润滑油这些措施均可防止或减轻主减速器齿轮的不正常磨损。
2、主减速器常见故障分析
(1)主减速器齿轮早期磨损的实践表明,主减速器齿轮产生早期磨损的真正原因,往往不是齿轮本身的质量问题,必须对其工作条件进行综合分析。造成螺旋锥齿轮和斜齿圆柱齿轮早期磨损的原因,分析起来大致有以下几个方面:
①主、从动螺旋锥齿轮和斜齿圆柱齿轮啮合间隙过小;
②齿面接触位置调整不当;
③使用、维护或修理中,未按出厂要求加用润滑油;
④各轴承预紧度调整过紧,行驶过程中发热,造成油温过高,润滑油粘度下降,油膜的强度也遭到削弱;
⑤后桥壳通气孔被堵塞,使桥壳内部在工作温度影响下压力增加,迫使润滑油从各密封衬垫处渗漏,或自油封处甩出,造成润滑油缺乏;
⑥主减速器壳与后桥壳连接螺栓松动,或未按规定扭矩拧紧,或两者接合面处密封衬垫被挤破,使润滑油泄漏;
⑦汽车在使用过程中长期超载或超速行驶;
⑧修理及装配过程中,混入了外界磨料颗粒等;
(2)主减速器异响
造成主减速器异响这一故障的原因,可归纳为以下几类:
①进入啮合的齿轮副齿侧间隙过小或啮合不良;
②齿轮的啮合间隙过大;
③各处轴承因长期使用,造成磨损松旷,或因紧固螺栓、螺母松动造成轴承松旷,齿轮或轴承发生轮齿断裂或轴承破碎;
④由于各种原因所造成的润滑油不足或油的粘度太小;
⑤在内应力、外载荷和使用温度影响下,主减速器壳发生变形,使齿轮的相互位置关系变动,正确啮合关系遭到破坏。
造成主减速器异常响声的各种原因,分析起来比较容易,但具体确定时需要较多的故障诊断经验,需结合不同的汽车运行情况,综合加以判断,其中涉及到齿轮时,如不能通过调整解决问题,则大多需要更换齿轮,且成对地更换。
(3)主减速器壳过热
主减速器壳,尤其是内部装有轴承处出现过热,主要是由以下原因造成的:
①各支承轴承装配时,轴承预紧度过高;
②各齿轮副啮合时齿轮间隙过小;
③各种原因造成的润滑油不足或油的粘度太小;
④汽车使用中长期超速超载;
⑤主减速器壳在使用中因制造内应力、外载荷和温度等影响下,产生变形,使其上各承孔相互位置发生变化,轴承运行阻力增加。